钟罩炉碳排放监测与减排策略
更新时间:2025-07-16 点击次数:76
钟罩炉作为高温热处理核心设备,广泛应用于粉末冶金、陶瓷烧结、半导体材料制备等领域。其以电能或化石燃料(如天然气)为热源,运行中因化石能源燃烧、电力间接排放及工艺过程逸散,成为工业碳排放的重要来源。随着“双碳”目标推进,钟罩炉的碳排放监测与减排优化成为行业绿色转型的关键环节。
一、碳排放源解析:从能源消耗到工艺逸散
钟罩炉的碳排放主要源于三方面:
1.直接排放:以天然气为燃料时,燃烧产生CO₂(每立方米天然气约排放2kg CO₂);若采用煤炭,排放强度更高;
2.间接排放:电能驱动的加热元件(如电阻丝)依赖火力发电时,需计入电力全生命周期碳排放(我国电网平均碳排放因子约0.58kg CO₂/kWh);
3.工艺逸散:炉体密封不严导致保护气体(如N₂、Ar)泄漏,或高温下有机物挥发(如粘结剂分解),产生非CO₂温室气体(如CH₄、N₂O)。
实测数据显示,一台年运行3000小时的天然气钟罩炉,直接碳排放可达120~150吨CO₂e(二氧化碳当量),间接排放占比约30%~50%(取决于电力结构)。
二、减排策略:全链条协同优化
针对上述排放源,需从能源结构、设备升级与工艺创新三方面协同发力:
1.能源替代与能效提升:
采用电加热替代燃气加热,结合光伏、风电等绿电消纳,可减少直接碳排放;
升级高效燃烧器(如分级燃烧技术),优化空燃比至理论值±1%误差,降低过剩空气导致的无效排放;
集成余热回收系统(如烟气-水换热器),将排烟温度从300℃降至150℃以下,热效率提升15%~20%。
2.工艺革新与材料优化:
开发低温烧结工艺(如微波辅助烧结),降低峰值温度需求(降幅可达200~300℃),减少能源消耗;
采用无粘结剂成型技术或低挥发分粘结剂,减少有机物分解产生的逸散排放;
强化炉体密封设计(如磁流体密封+泄漏报警装置),将保护气体损耗率从5%降至1%以下。
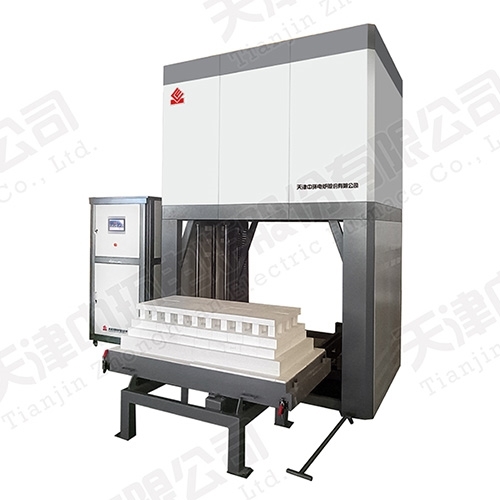
3.碳监测与数字化管理:
安装在线监测设备(如红外CO₂传感器、流量计),实时采集燃料消耗、电力使用及气体泄漏数据,接入企业碳管理系统;
基于生命周期评估(LCA)模型,量化原料运输、设备制造等隐含碳排放,制定全链条减排方案。
三、未来方向:低碳技术集成与标准完善
未来需进一步研发氢能燃烧、光热耦合等零碳热源技术,并推动行业碳排放核算标准统一(如ISO 14064认证),为钟罩炉低碳转型提供系统性支撑。
通过能源替代、工艺升级与数字化监测,钟罩炉的碳排放强度可降低40%~60%,助力行业实现绿色可持续发展目标。